Introduction
Traditional Product Lifecycle Management (PLM) systems have long served as the foundation for managing product data, engineering changes, and production workflows. However, these systems operate at a task level rather than a step level, meaning they provide high-level process control but lack granular, executable step-by-step guidance necessary for flawless execution on the production floor.
This gap between PLM design intent and real-world execution often leads to errors, misinterpretations, and inefficiencies in manufacturing. PROMAI bridges this gap by automating the creation of precise, step-by-step executable processes that integrate directly into the PLM workflow, ensuring that every instruction is atomic, verifiable, and error-proof.
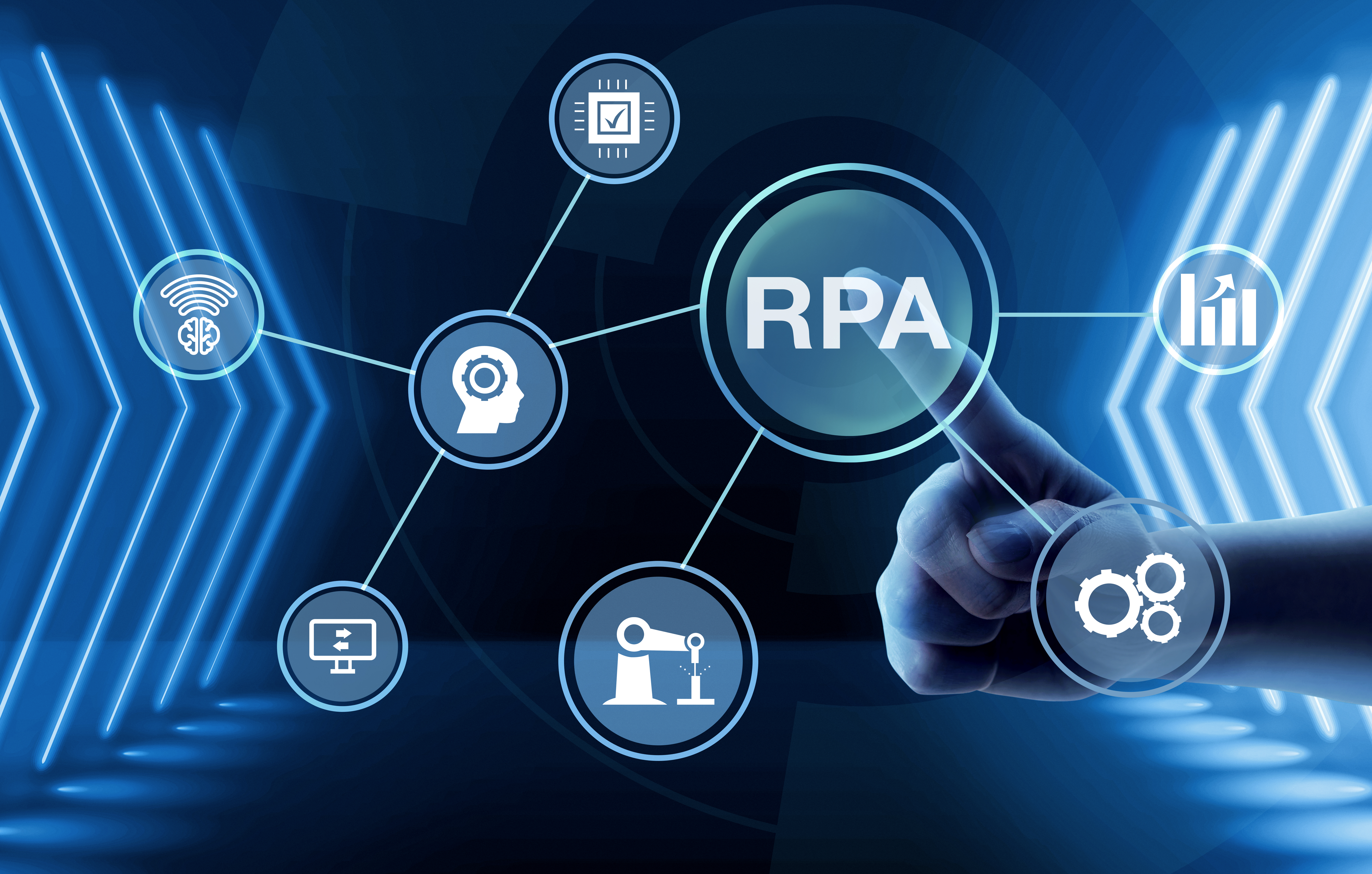
The Limitations of Traditional PLM Systems
While traditional PLM systems effectively manage product designs, engineering changes, and task-based workflows, they fall short in translating these tasks into detailed, executable production instructions.
This disconnect can lead to:
Misinterpretation of Tasks – Operators and production teams must manually interpret task-level instructions, leading to inconsistencies and human errors.
Lack of Granularity – PLM workflows define what needs to be done but not how to do it at each step.
Delayed Error Detection – Without real-time validation at the step level, errors may only be detected during quality control or after production is complete, leading to costly rework.
Inefficient Knowledge Transfer – Workforce training and standardization suffer due to reliance on implicit knowledge rather than structured, repeatable, and verifiable processes.While PLM has improved engineering collaboration and product data management, it does not prevent execution errors in real-time—a critical requirement for modern high-precision manufacturing environments.
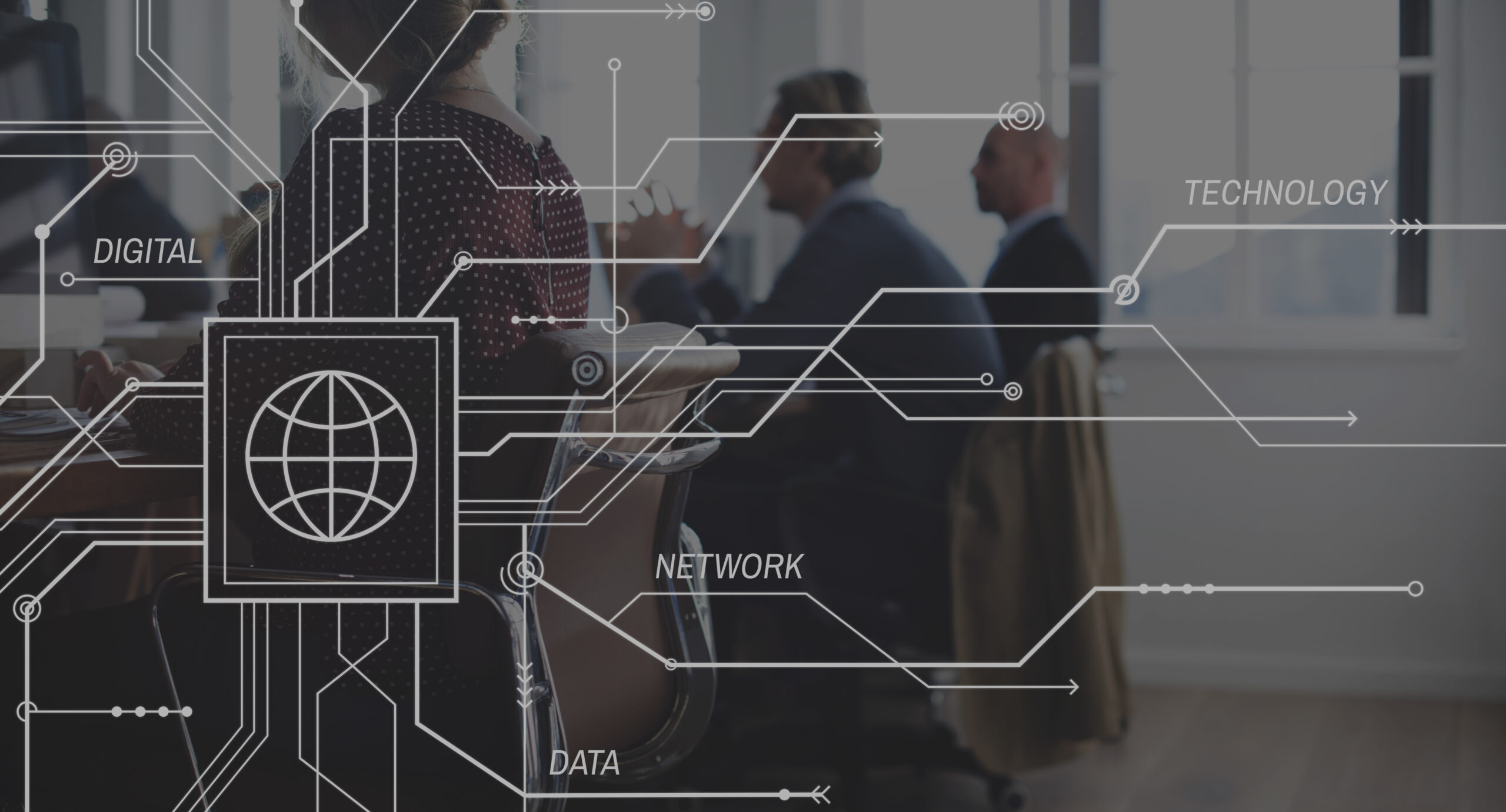
How PROMAI Enhances PLM
by Enabling Step-Level Execution
PROMAI transforms traditional PLM systems by integrating a real-time, executable workflow engine that translates high-level PLM tasks into step-by-step, verifiable execution processes.
How PROMAI Works:
Automated Process Generation – PROMAI automatically converts PLM task-level instructions into granular, step-by-step executable work instructions tailored for the production line.
Atomic Execution & Verification – Each step is delivered as a precise, verifiable instruction, preventing errors and ensuring compliance with engineering specifications.
Real-Time Guidance for Operators – Instead of vague task descriptions, workers receive interactive, visual step-by-step instructions with built-in validation mechanisms.
Error Prevention & Compliance – PROMAI ensures that every step is validated before the next step begins, eliminating the risk of accumulating mistakes.
Seamless PLM Integration – PROMAI acts as an intelligent execution layer within the PLM ecosystem, ensuring that engineering intent is accurately carried out on the production floor.
By integrating PROMAI Suite into PLM systems, manufacturers eliminate process ambiguity, reduce production errors, and enhance execution consistency across all production lines.
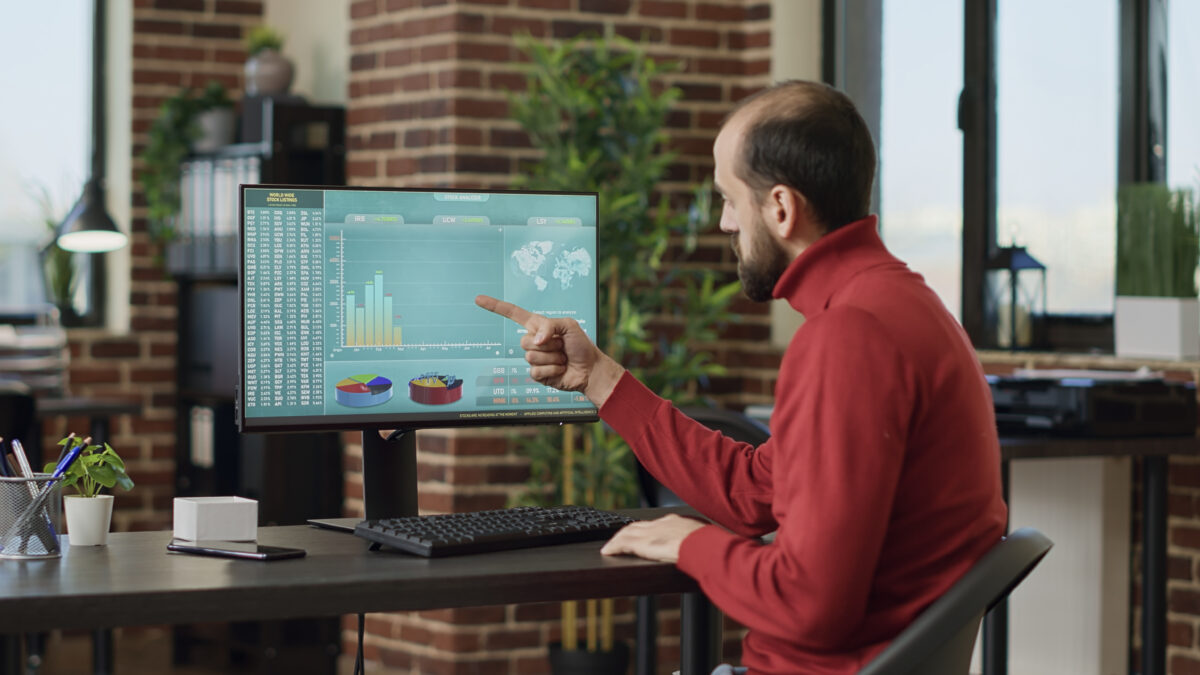
The Future of PLM: From Task-Based to Step-Based Execution
Manufacturing environments are becoming increasingly complex, requiring precision, standardization, and real-time adaptability. Traditional PLM systems remain essential for managing product data and workflows, but they must evolve to include executable step-by-step guidance to truly ensure error-free production.
With PROMAI Suite, manufacturers can:
Turn static PLM workflows into dynamic, error-proof execution processes.
Reduce human interpretation errors through automated, interactive instructions.
Improve traceability, compliance, and quality assurance from design to production.
Ensure that engineering intent is flawlessly translated into production reality.